Abrasive wheels are used in many different industries for a variety of purposes. They can be made from a variety of materials, including aluminum oxide, silicon carbide, and diamond. Each type of abrasive wheel has its own set of benefits and drawbacks.
Depending on the application, the type of abrasive wheel that is best suited may vary.
There are a few different tests that should be performed on abrasive wheels to ensure they are safe for use. These tests include:
-A visual inspection of the wheel to check for cracks, chips or other damage.
-A balance test to ensure the wheel is not unbalanced and will not vibrate excessively when in use.
-A hardness test to make sure the wheel is made of a material that will not break down too easily under heavy use.
Compressed Air Can Be Used for Cleaning As Long As It’S Less Than 30 Psi
If you’re looking for a way to clean something without using harsh chemicals, compressed air may be the answer. It’s safe to use on most surfaces and is less likely to cause damage than other cleaning methods. However, it’s important to make sure that the air pressure is less than 30 psi, as anything higher could potentially damage the surface you’re trying to clean.
Jointer Should Be Fitted With Which of the Following Types of Guards
There are several types of guards that can be fitted to a jointer, and the type of guard that should be used depends on the application. The most common types of guards are:
1. Fixed Guards: These guards are permanently attached to the jointer and cannot be removed without tools.
They provide good protection for the operator but can limit visibility and access to the workpiece.
2. Adjustable Guards: These guards can be adjusted to different positions, depending on the needs of the operator. They offer good protection while still allowing good visibility and access to the workpiece.
3. Interlocked Guards: These guards are designed so that they cannot be removed unless the power is turned off and the blades are completely stopped. This provides maximum safety for the operator but can make it difficult to change settings or access the workpiece.
Has Overall Responsibility for Compliance With Osha Regulations
When it comes to keeping your workplace safe, OSHA compliance is key. But who has overall responsibility for making sure your business is up to snuff?
The short answer is that the employer has the ultimate responsibility for complying with OSHA standards.
However, there are a few caveats to this rule.
First and foremost, employers must provide their employees with a safe and healthful workplace. This includes ensuring that all equipment and machinery are properly maintained and that any potential hazards are identified and corrected in a timely manner.
In addition, employers must train their employees on how to safely perform their jobs and use any necessary safety gear. They must also develop and implement emergency procedures in case of an accident or other hazard.
Finally, employers must keep accurate records of injuries and illnesses that occur in the workplace.
These records can be used to identify trends and correct any potential problems before they cause serious harm.
While the employer has the ultimate responsibility for compliance, employees also have a role to play in keeping the workplace safe. They should report any unsafe conditions or practices to their supervisor immediately so that corrective action can be taken.
Employees should also participate in safety training programs and follow all safety rules while on the job.
Appropriate Switches for Belt Sanders are Constant Pressure
Belt sanders are one of the most versatile and powerful tools in any woodworker’s arsenal. They can be used for a variety of tasks, from shaping edges to removing paint or varnish. But with all that power comes the need for control, which is where switches come in.
There are two main types of switches available for belt sanders: constant pressure and trigger. Constant pressure switches keep the sander running as long as you’re holding down the switch, while trigger switches only run when you’re actively pressing the trigger.
So which type of switch is best for a belt sander?
It really depends on your needs and preferences. If you need to be able to adjust the speed on the fly, then a trigger switch is probably your best bet. However, if you want maximum control over the sander, then a constant pressure switch will give you that extra level of precision.
Powder Actuated Tools Should Never Be Used on What Kind of Materials
When it comes to powder-actuated tools, there are certain materials that you should never use them on. These tools are powerful and can cause serious damage if used incorrectly. Here is a list of materials that you should never use a powder-actuated tool on:
1. Glass – Glass is fragile and using a powder-actuated tool on it will cause it to shatter. This can be extremely dangerous as shards of glass can fly everywhere and cause serious injuries.
2. Thin Metal – Thin metal is also fragile and using a powder-actuated tool on it will cause it to bend or break.
This could create sharp edges that can cut or puncture skin.
3. Stone – Stone is very hard, but it is also brittle. Using a powder-actuated tool on stone can cause it to crack or splinter, which can again be very dangerous as flying debris could injure someone nearby.
4. Concrete – Concrete is extremely tough, but it too can be damaged by a powder-actuated tool if used incorrectly. The tool can chip or crack the concrete, which could create hazardous conditions for anyone walking or standing nearby.
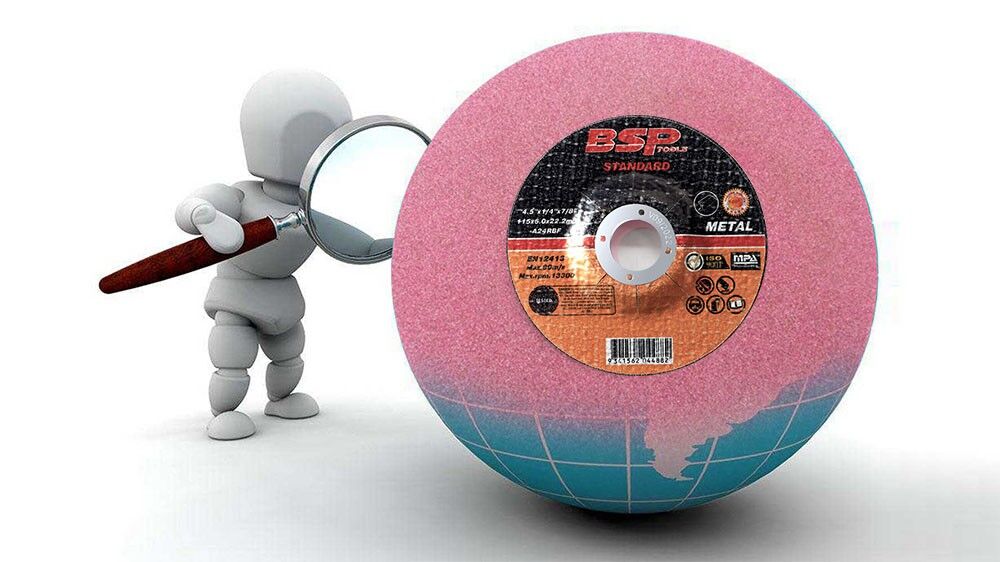
Credit: binictools.com
What Test Should Be Performed on Abrasive Tools?
abrasive tools, such as grinding wheels, sandpaper, and honing stones, are made of natural or synthetic materials that are harder than the workpiece material. When these tools are used to cut or shape metal, they can create sparks that may contain harmful metals. To ensure that these sparks do not pose a health hazard, OSHA recommends that employers test the abrasive materials before using them.
One way to test for potential hazards is to use a spark-testing machine. This machine uses high-speed photography to capture the sparks emitted when an abrasive tool is used. The photos can then be analyzed to determine if any harmful metals are present in the sparks.
Another way to test for potential hazards is to use a chemical analysis kit. This kit contains chemicals that change color when they come into contact with certain metals. By testing the abrasive material with this kit, employers can determine if any of the harmful metals are present.
By performing these tests, employers can ensure that their employees are not exposed to any unnecessary health risks when using abrasive tools.
What are the Best Practices When Working With Abrasive Wheel Tools Osha Quizlet?
Abrasive wheel tools are power-driven tools that use abrasive wheels to cut, grind or clean metal surfaces. There are many different types of abrasive wheel tools available on the market, each designed for a specific purpose. However, all abrasive wheel tools share one common goal: to quickly and effectively remove material from a workpiece.
When using any type of abrasive wheel tool, it’s important to follow best practices in order to ensure safety and minimize the risk of injury. Here are some tips to keep in mind:
1. Always wear appropriate personal protective equipment (PPE).
This includes eye protection, gloves and hearing protection if necessary.
2. Inspect your abrasive wheel before each use. Make sure it is not damaged and that the speed rating is appropriate for the task at hand.
3. Do not exceed the recommended speed for your particular abrasive wheel tool. Doing so can cause the wheel to break apart and create flying debris which can be extremely dangerous.
4. Use only wheels that have been specifically designed for the material you’re working with.
Using an incorrect wheel can damage both the tool and the workpiece.
5 Keep both hands on the tool while it’s in operation.
Why Must Abrasive Grinding Wheels Be Inspected?
Abrasive grinding wheels must be inspected for cracks, chips or other damage before each use. If a wheel is damaged, it should be replaced immediately. Inspecting your abrasive grinding wheels regularly can help prevent accidents and injuries.
Can Compressed Air Be Used for Cleaning As Long As It is Less Than 30 Psi?
Yes, compressed air can be used for cleaning as long as it is less than 30 psi. This is because compressed air is a very effective way to remove dirt, dust, and debris from surfaces. When using compressed air for cleaning, it is important to use the proper nozzle and pressure setting to avoid damaging the surface being cleaned.
Grinder & Abrasive Wheel Safety Training (Standard Version)
Conclusion
Abrasive wheels are a key component in many manufacturing processes. While they can be very effective, it is important to ensure that they are tested regularly to avoid accidents. There are a few different tests that should be performed on abrasive wheels, including:
-A visual inspection of the wheel itself, looking for any cracks or damage.
-A test of the speed at which the wheel rotates. This should be done with a tachometer.
-An assessment of the balance of the wheel. This can be done by hanging the wheel from a central point and seeing how it spins.